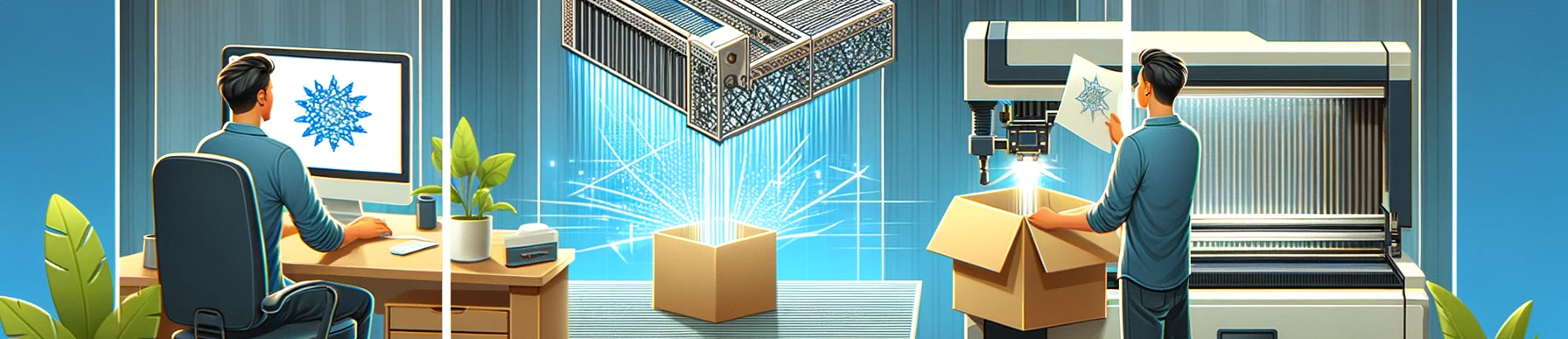
How it works...
Material We Process
-
Mild Steel
We can currently cut mild steel from .95mm to 12mm, with thicker capabilities coming soon!
-
Aluminium 5052
We offer 5052 grade aluminium as it allows welding and bending, we currently cut up to 5mm aluminium.
-
Stainless 304
We currently cut and ship 304 grade stainless steel up to a maximum thickness of 5mm!
Surface Finishes
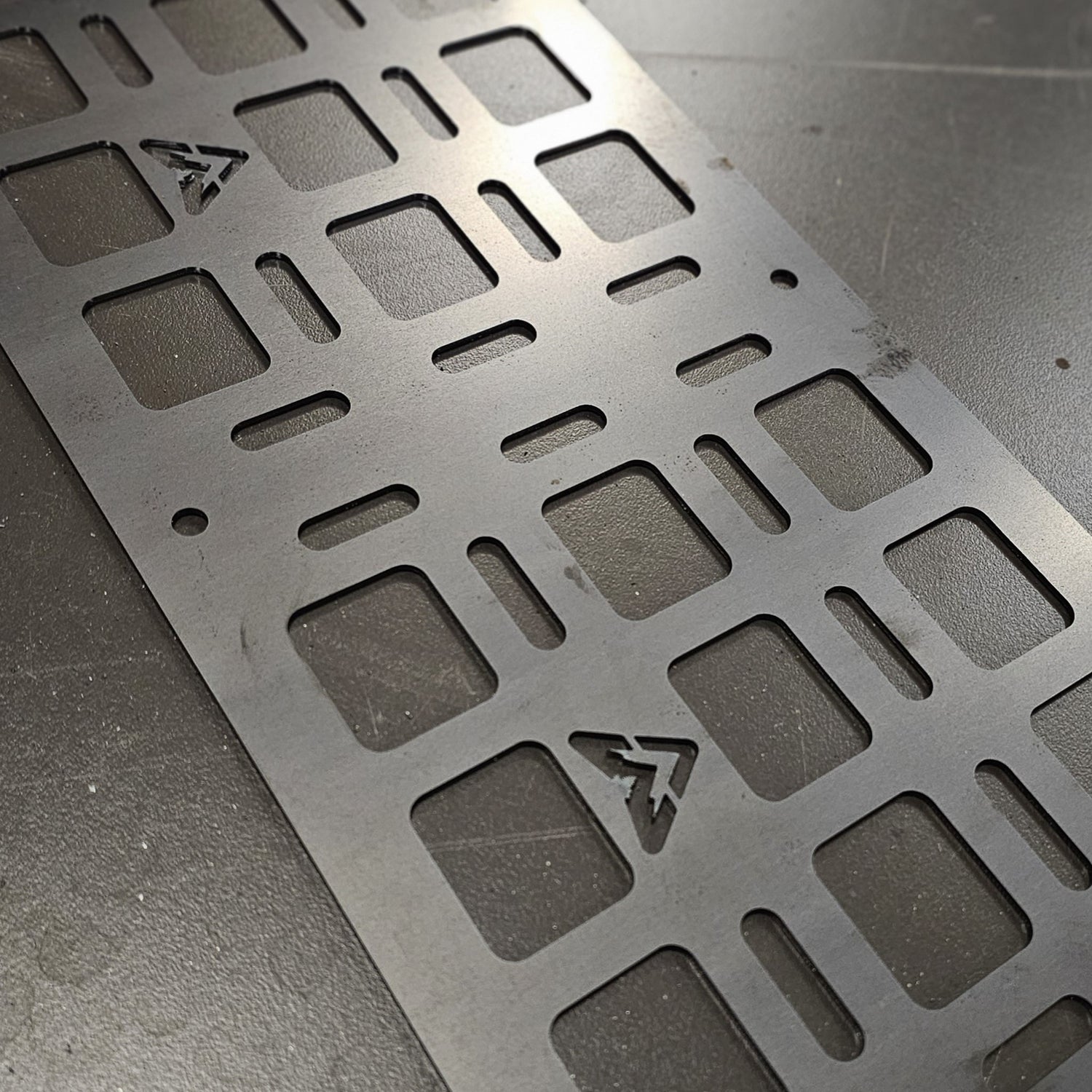
Parts Finish
Mild Steel
Mild steel is lightly DA sanded to remove any small edge remnants from the cutting process, due to the nature of mild steel, you cant really tell its been surface finished.
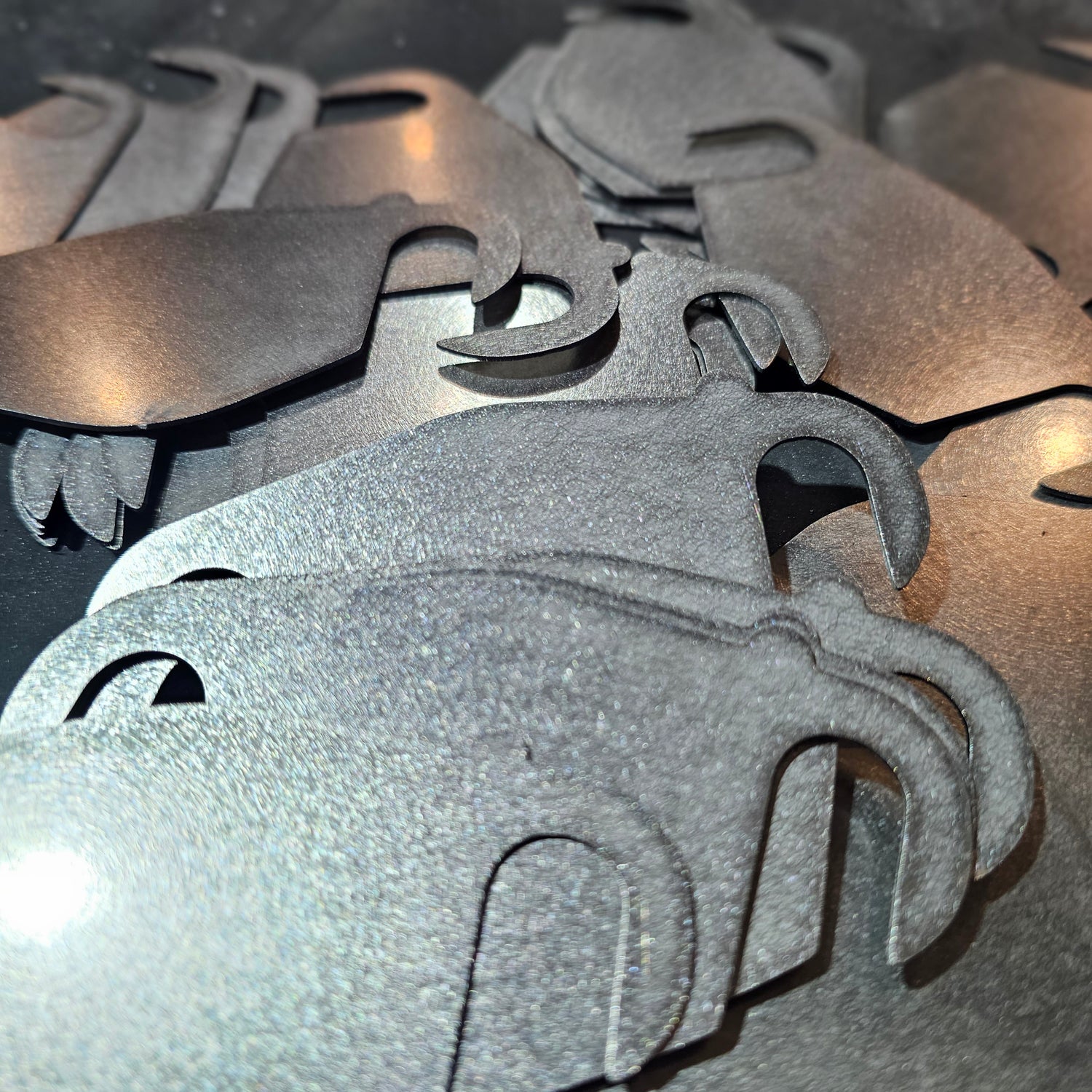
Parts Finish
Stainless Steel
Stainless steel is DA sanded prior to shipping to give the surface a uniform appearance and remove any edge remnants.
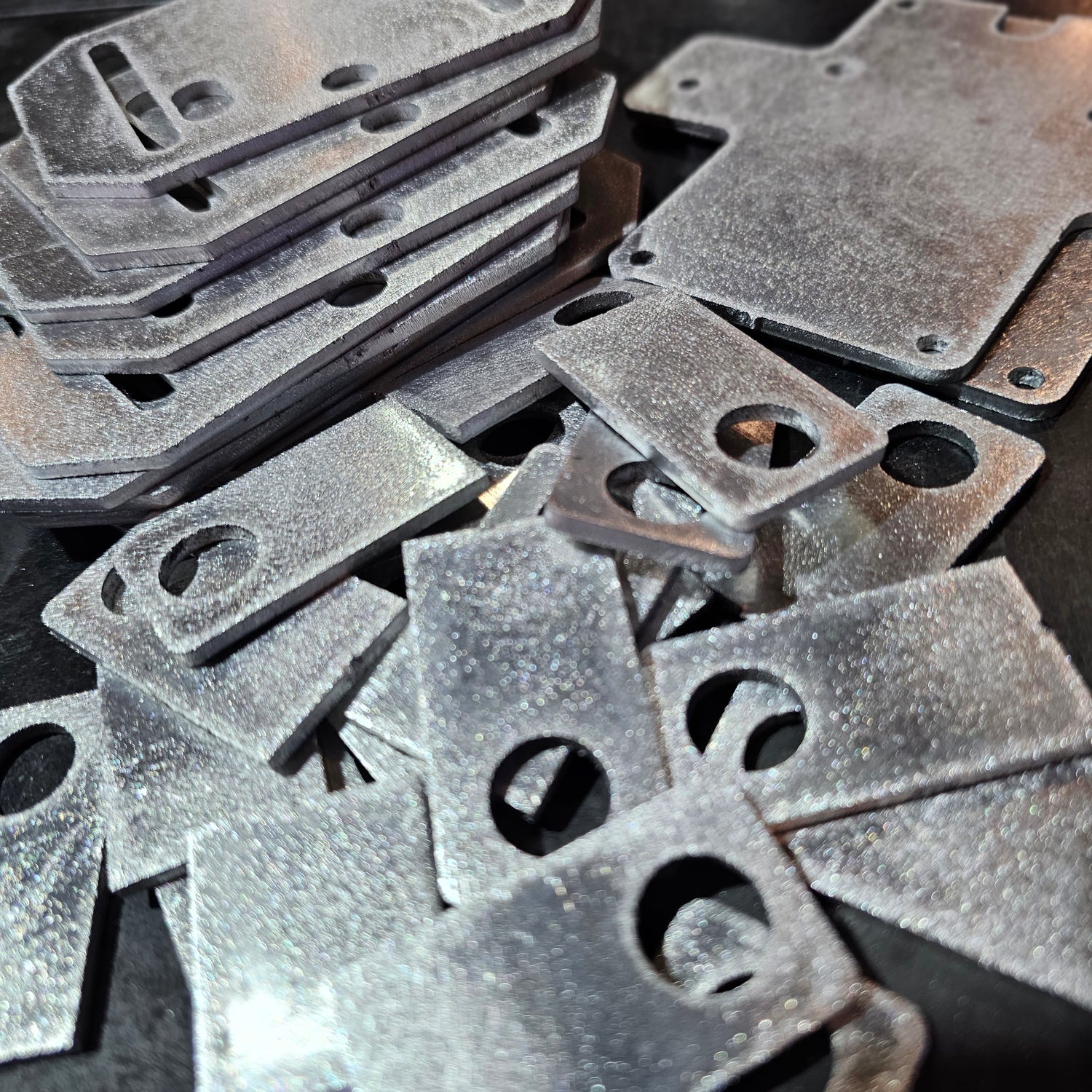
Parts Finish
Aluminium
Aluminium is given a DA sand to remove any large burrs, some attention may need to be given to end finish the part depending on end application.
Part Design Tips!
When designing parts for laser cutting, it's crucial to adhere to specific size guidelines to ensure structural integrity and readability. Avoid using holes that are smaller than the thickness of the material or smaller than 3mm. For lettering, make sure the height exceeds 12mm, with at least 2mm of spacing between letters; more spacing is preferable to enhance legibility. Additionally, any bridges added to prevent the centers of letters from falling out should be a minimum of 1.5mm wide to ensure they remain intact during cutting.
When incorporating holes, position them at least a few millimeters from the edge, ensuring there is a boundary of at least 3mm around each hole. Avoid placing holes within 12-15mm of a bend, as this can lead to distortion when the material is folded. For optimal results, it's advantageous to add material wherever possible, as this reduces the risk of heat distortion during the cutting process and enhances the overall durability of the finished part. By following these guidelines, you can create designs that are not only visually appealing but also practical and functional.
How the Process Works!

Step 1:
Laser cutting your ideal sheet metal part has never been easier. With our intuitive interface, simply create your design and upload the .DXF file effortlessly. Choose from a variety of materials to suit your specific needs, whether it's stainless steel, aluminium, or mild steel. Once uploaded, our system instantly generates a quote, providing you with transparency and efficiency in the process. Say goodbye to lengthy waits and uncertain pricing—get your project started with precision and speed, all at your fingertips.

Step 2:
Upon receiving your file, we set to work with precision and expertise, cutting your part from the material you've specified using our state-of-the-art laser cutting machines. Our advanced technology ensures accuracy down to the finest detail, guaranteeing that your design is executed flawlessly. Trust in our commitment to quality craftsmanship as we bring your vision to life with the utmost precision and efficiency.

Step 3:
Once your design has been meticulously cut to perfection, we take care to package it securely, ensuring its safe journey to your doorstep. With our expedited delivery, rest assured that your package will be handled with the utmost care and attention. Our commitment to quality extends beyond production, encompassing every step of the process until your order reaches you promptly and securely.

Step 4:
As the package arrives, you're eager to unbox your custom-made parts. With excitement, you tear open the packaging to reveal the precision-crafted pieces inside that you helped create. Each part is a testament to your design, ready to be utilised in your project. With a sense of fulfilment, you start incorporating them, confident in their performance and the seamless process from design to delivery.
Your Intellectual Property...
Here at Laser Corp, your intellectual property remains yours!
Never ever, under no circumstances, will we use, recreate, or distribute our valued customers files.
We do however love to see the parts in use, so ensure you tag us on your socials!